Powder coating is a dry finishing process where electrically charged powder is sprayed onto a surface and then heated to create a durable, protective coating. It is more than just a colorful finish—it’s a sophisticated process rooted in advanced science and engineering. In this blog post, we explore how powder coating works by focusing on the electrostatic principles that make it both efficient and eco-friendly.
What Is Powder Coating?
Powder coating is a dry finishing process that uses a finely ground mixture of pigment, resin, and additives instead of traditional liquid paints. The result is a durable and aesthetically pleasing coating applied to metal parts and other substrates. Powder coating is primarily used on metal items, especially those exposed to heavy use. Advances in technology, like UV-curable powders, enable coatings on materials such as plastics, composites, and carbon fiber.
The Role of Electrostatics in Powder Coating
Powder coating has forever changed the way we finish metal surfaces by combining environmental friendliness with exceptional durability and uniformity. At the core of the powder coating process is the power of electrostatics. The electrostatic forces attract the charged particles toward the grounded substrate, however, some particles may not end up exactly where desired, potentially leading to coverage challenges and non-uniform finishes. At coatingAI, we have developed Blueprint™ OS, a system designed to optimize powder coating processes and address this specific challenge, among other improvements. Keep reading this piece to learn more about how we overcome this issue, or visit our onboarding information page to learn more about the demo and onboarding process for Blueprint™ OS.
Charging the Powder
Before application, the powder particles are given an electrical charge. This is typically done using a specialized spray gun equipped with an electrode. Two common methods are corona charging and triboelectric charging
Corona Charging
Corona charging is the most widely used method in powder application. In this process, the powder is dispersed into an air stream, forming a cloud as it exits the spray gun. As the particles travel through the charged corona field at the gun’s tip, each one is imbued with a strong negative charge.
- A high-voltage, low-current electrical field is generated at the tip of a specialized spray gun.
- This electrical field ionizes the air around the electrode.
- As the powder particles pass through this ionized cloud, they pick up a negative charge.
- The result is a uniform charge on each particle, setting the stage for a precise and efficient application.
Triboelectric Charging
The underlying principle of this charging process is to achieve close contact and, thus, efficient friction between polymer and carrier particles inside the charging device accompanied with triboelectric charge transfer.
- The powder is forced through a specially designed tube where it rubs against a surface.
- This friction generates a charge on the particles.
- Although less common than corona charging, triboelectric methods are particularly useful in certain applications where precise control over the charge is needed or where corona charging might present challenges.
Both of these charging methods ensure that each particle carries an electrostatic charge, setting the stage for precise deposition.
Attraction to the Grounded Substrate
Once charged, the powder particles are sprayed onto the part that needs coating. When the charged powder leaves the spray gun, it’s not simply floating in space—it’s under the influence of a well-defined electric field created by the grounded substrate.
The part is connected to a ground (i.e., it’s electrically neutral or positively charged), which creates a strong electrostatic attraction. According to Coulomb’s law, oppositely charged objects attract. This principle causes the negatively charged powder to adhere uniformly to the surface of the grounded object—even into hard-to-reach areas and around curves.
Role of Grounding in Achieving Uniform Coating
- Uniform Charge Distribution:
A well-grounded substrate acts like a vast reservoir that can quickly dissipate any excess negative charge. As a result, the entire surface is maintained at a uniform (or nearly uniform) potential. This uniformity is critical for achieving even coverage—the powder particles are attracted evenly, ensuring a smooth, consistent finish even on complex geometries. - Minimizing the Faraday Cage Effect:
Although the fundamental attraction is dictated by Coulomb’s law, the geometry of the substrate also matters. In recessed or sharp-cornered areas, the distribution of the induced charge might not be perfect, sometimes leading to the Faraday cage effect where powder has difficulty entering these zones. However, a solid grounding and proper substrate design help to minimize these issues by maintaining a consistent positive potential across the entire surface.
Distance and Strength of the Attraction
- Proximity is Key:
Because the force is inversely proportional to the square of the distance between the charged powder and the substrate, spraying the powder close to the surface maximizes the attractive force. This means that even if some powder is initially deflected or directed at an angle, as long as it is within a short distance, the electrostatic force will pull it in for adhesion. - Efficient Material Use:
This strong and localized attraction is why the electrostatic process is so efficient—up to 95% or more of the powder ends up on the substrate with minimal waste.
Overcoming Powder Coating Challenges with coatingAI
While the electrostatic process for powder coating is highly effective, it’s not without its challenges. Achieving a uniform finish is often difficult due to the complex interplay of three key forces: the electrostatic field, the airflow from spray guns, and gravity. Each of these forces affects particles differently based on their size, charge, and trajectory.
This complexity means that achieving a perfectly even coating isn’t always straightforward. Factors like part geometry, air turbulence, electrostatic field strength, and variations in particle size can lead to uneven distribution or excessive overspray.
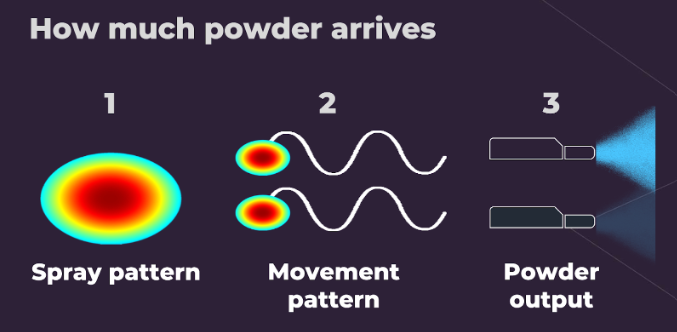
The powder coating process ultimately comes down to three key factors: how much powder is released from the spray guns, how effectively the airflow and electrostatic field guide it toward the target surface, and how much of it successfully adheres to the grounded substrate. Each step in this process is influenced by variables such as particle size, charge distribution, air turbulence, and part geometry, all of which impact the overall efficiency and uniformity of the coating.
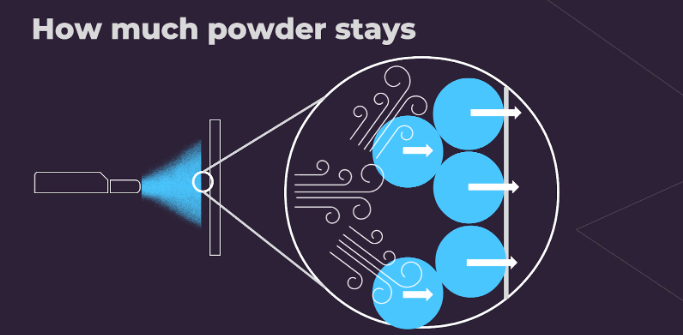
Each particle, depending on its size, interacts with the three aforementioned forces differently. Larger particles, due to their mass, are more affected by gravity and tend to settle quickly rather than adhering to the surface. Medium-sized particles are most influenced by the electrostatic field, which helps attract and hold them onto the grounded substrate. Meanwhile, the smallest particles predominantly follow the air flow, making them more difficult to control and potentially leading to uneven coverage. Airflow plays a crucial role in guiding the powder but can also push particles away if not properly controlled.
Achieving uniform coverage requires a delicate balance—ensuring that electrostatics provide enough attraction for the particles to stick while optimizing airflow to direct them effectively without disrupting adhesion. Due to the complexity and numerous variables in the process, the resulting powder coating finish is often extremely non-uniform.
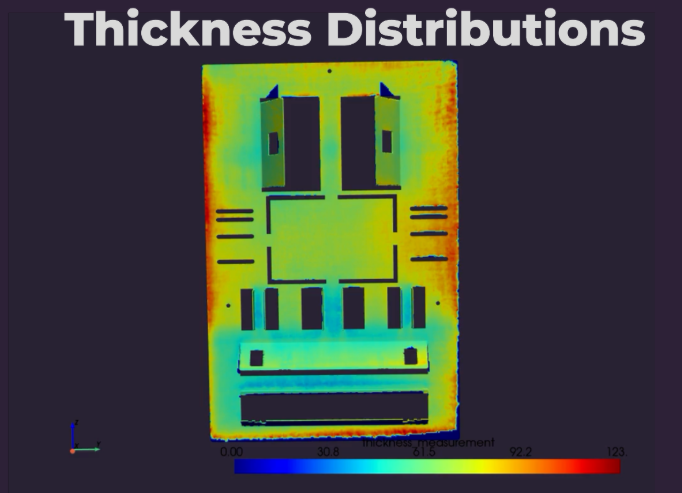
At coatingAI, we have developed Blueprint™ OS, an advanced system that effectively addresses these challenges. By integrating artificial intelligence into key stages of the powder coating process we are ensuring a consistent and high-quality finish.
This intelligent system adjusts reciprocator settings and calibrates each gun to its optimal spray pattern, compensating for variables like particle size, charge distribution, and air flow. As a result, Blueprint™ OS minimizes issues like uneven distribution and excessive overspray, leading to reduced powder consumption and enhanced coating uniformity.
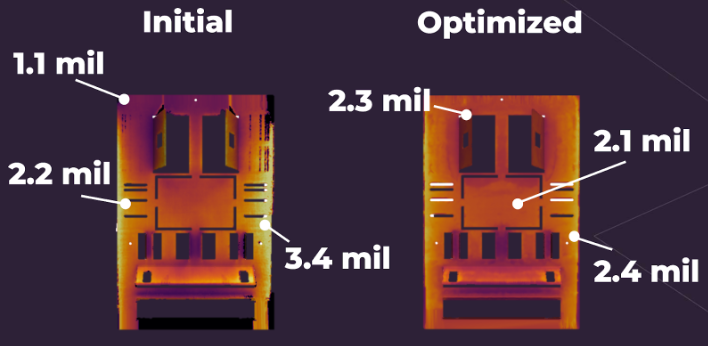
If you want to learn more about optimizing the interaction between electrostatics, airflow, and gravity to improve coating uniformity, visit our page where we explain the spray calibration step of our Blueprint™ OS system.
From Powder to Protective Film: The Curing Process
After the powder is applied, the coated object enters a curing oven. Here’s what happens next:
- Melting and Flowing: The powder is heated until it melts and flows into a smooth, continuous film. The precise temperature and time depend on the specific powder formulation and the thickness of the coating.
- Chemical Crosslinking: For thermosetting powders, the heat triggers a chemical reaction called crosslinking. This reaction forms a strong, three-dimensional polymer network that bonds the powder into a hard, resilient finish.
- Cooling: Once cured, the part is allowed to cool, solidifying the coating and ensuring long-lasting durability.
This curing process not only secures the powder in place but also enhances its resistance to impact, abrasion, and environmental degradation.
Advantages of the Electrostatic Powder Coating Process
The unique combination of electrostatic application and thermal curing offers several advantages:
- Efficiency: The electrostatic charge minimizes overspray, allowing up to 95% of the powder to adhere to the surface.
- Uniformity: Even complex shapes receive a consistent and even coating, reducing the need for touch-ups.
- Eco-Friendly: Without the use of solvents, the process significantly reduces harmful emissions and hazardous waste.
- Durability: The cured powder coating forms a robust protective layer that resists chipping, scratching, and corrosion.
Innovations on the Horizon
The powder coating industry continues to innovate. New powder formulations, improved charging technologies, the usage of AI for powder coating optimization, and advanced curing methods (such as UV curing) are driving efficiency and expanding the range of materials that can be powder coated. These innovations not only enhance performance but also contribute to more sustainable manufacturing practices.
Powder Coating is Here to Stay
Powder coating’s magic lies in its smart use of electrostatic forces—a blend of physics and chemistry that transforms dry powder into a resilient, high-performance finish. This process not only delivers superior aesthetics and durability but also supports eco-friendly manufacturing. Whether you’re involved in automotive, architectural, or industrial applications, understanding the science behind powder coating can help you appreciate the technology that keeps our products looking great and performing well for years to come.
Explore more about our cutting-edge coating technologies and solutions at coatingAI.